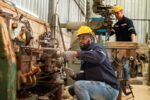
Visit Our Sponsors |
|
|
|
|
|
|
|
|
|
|
|
|
|
|
|
|
|
|
|
|
|
|
|
|
|
|
|
|
Photo: iStock/LeoPatrizi
Analyst Insight: The information and communications technology (ICT) sector has built its complex and cost-driven supply chains on fragile foundations, using millions of vulnerable workers. With rising regulatory scrutiny and growing ESG expectations, companies that fail to implement robust human rights due diligence not only endanger workers but generate systemic risks for businesses and investors.
The ICT sector is often seen as a beacon of innovation. But look beneath the surface and you will see that it is built on fragile foundations. The sector is a transnational ecosystem of buyers, suppliers, manufacturers and service providers. All these interactions and transactions are powered by the labor of millions of assembly workers. While a boon for employment and a key contributor to GDP, particularly among developing economies, these complex supply chains are easily disrupted. When workers face instability, exploitation or burnout, the entire system becomes vulnerable to breakdowns.
Production practices that break the manufacturing process down into microtasks in far-flung locations means disruption in one part of the chain has profound repercussions for others. So, what appears as a cost-effective model is actually a precarious structure balancing on the backs of underpaid and invisible workers. This fragility underscores the need for robust human rights due diligence that identifies and deals with risks to workers and communities.
For decades, ICT companies have pushed for lower costs, creating supply chain dynamics where suppliers compete fiercely to offer lowest prices. The cost of this race to the bottom should not be measured in price per unit but human lives.
While it may boost brands’ margins in the short term, the unintended consequences for workers — and therefore the supply chain itself — are severe. Suppliers, desperate to meet price demands and recoup money where they can, may suppress wages, adopt oppressive management practices and enforce excessive working hours.
KnowTheChain research found that despite the proliferation of no-recruitment-fee policies adopted by brands, most fail to show how these policies are implemented to ensure workers don’t bear the cost upfront with the hope of being reimbursed later, which may or may not happen. This situation can leave them at risk of debt bondage and forced labor.
The solution: responsible purchasing practices that factor in the true cost of ethical production. Companies must commit to fair payment terms and transparent pricing that accounts for living wages and ethical recruitment. Myopic cost-cutting may deliver immediate savings, but it ultimately weakens the entire supply chain, increasing the risk of disruption, reputational damage and financial loss.
The just-in-time production model is celebrated for its efficiency. By keeping inventory low and production lean, companies minimize costs and maximize responsiveness. But JIT’s efficiency comes at a cost. When orders surge, factories demand immediate overtime from workers, often without proper compensation or consent. When demand drops, temporary staff — many of them vulnerable migrants — are first to be dismissed. The JIT model creates flexibility for brands but breeds instability for workers. Prioritizing short-term cost reductions over long-term stability exposes companies to supply chain disruptions, and further obscures accountability within supply chains by incentivizing illegal subcontracting by suppliers scrambling to meet unrealistic deadlines.
A more responsible production model — one that balances efficiency with respect for human rights — is possible. Companies can move beyond a short-term transactional approach to their suppliers and foster long-term relationships that prioritize stability over relentless cost-cutting. Clear commitments to improved production planning and investment in supplier capacity-building can transform supply chains from exploitative to resilient.
The right to organize, bargain collectively and work free from retaliation is fundamental to worker well-being. Yet, the ICT sector remains one of the worst performers in this regard. The latest KnowTheChain research found that 93% of ICT companies do not disclose efforts to support and enable freedom of association for supply chain workers. This is not just a failure of ethics; it is a failure of business sense.
When workers feel secure in their employment — when they have mechanisms to voice concerns, negotiate fair conditions and seek remedy for grievances — they are more engaged and productive, and less likely to leave. Conversely, a workforce that fears speaking out suffers in silence until exploitation reaches a breaking point, leading to factory shutdowns, strikes and severe reputational damage for brands.
The dangers of failing to implement robust due diligence practices are real, immediate and increasingly costly. With Europe introducing mandatory human rights due diligence laws, investor scrutiny on labor rights risks and its impact across supply chains is rising. Any company that ignores human rights risks is not simply being unethical, it is creating a business liability.
RELATED CONTENT
RELATED VIDEOS
Timely, incisive articles delivered directly to your inbox.